Proper electric motor preventive maintenance is crucial for ensuring the longevity and optimal performance of your electric motors. By taking a proactive approach, you can avoid costly breakdowns, extend the lifespan of your equipment, and maintain productivity in your operations.
The Importance of Electric Motor Preventive Maintenance
Regular inspections, lubrication, and timely repairs are the cornerstones of an effective motor preventive maintenance program. Neglecting these essential tasks can lead to premature motor failure, increased energy consumption, and unplanned downtime – all of which can have a significant impact on your bottom line.
Investing in preventive maintenance is a smart business decision. It allows you to stay ahead of potential issues, plan maintenance activities around your production schedule, and minimize the risk of unexpected disruptions. The small time and resources spent on preventive care will pay off in the long run through improved reliability, efficiency, and cost savings.
Common Motor Issues and How Preventive Maintenance Can Address Them
Proper preventive maintenance is essential for keeping your motors running smoothly and efficiently.
Below is a list of some of the most prevalent motor problems and how a robust preventive maintenance plan can help mitigate them.
Bearing Failure: Worn or damaged bearings are a leading cause of motor failure. Regular bearing inspection, lubrication, and replacement can prevent premature bearing wear and extend the motor’s operational lifetime.
Winding Insulation Breakdown: Over time, the insulation on motor windings can deteriorate, leading to short circuits and burnouts. Routine testing and maintenance of the winding insulation can identify and address issues before they become critical.
Rotor Bar Cracking: Cracks in the rotor bars can cause uneven current distribution and reduced motor efficiency. Proactive monitoring and repair of rotor bar issues can help maintain optimal motor performance.
Vibration and Misalignment: Excessive vibration and misalignment can put significant stress on motor components, leading to accelerated wear and tear. Implementing a vibration analysis program and ensuring proper shaft alignment can mitigate these problems.
Motor preventive maintenance with the AT7 by ALL-TEST Pro.
Proven Strategies for Implementing an Effective Electric Motor Preventive Maintenance Program
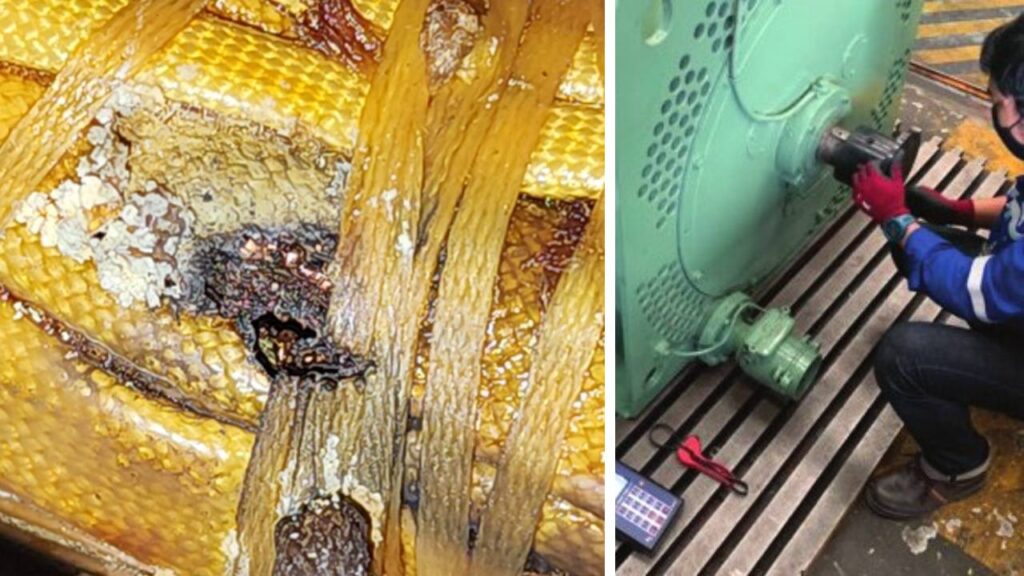
A well-designed electric motor preventive maintenance program is essential for maximizing the lifespan and efficiency of your equipment. Here are the proven strategies you need to implement an effective preventive maintenance program:
Establish a Detailed Inspection Routine: Regularly inspect your motors for signs of wear, damage, or improper lubrication. This allows you to identify and address issues before they escalate into major problems.
Implement Scheduled Maintenance: Create a detailed maintenance schedule that outlines the specific tasks and frequencies required for each motor. Stick to this schedule religiously to keep your equipment in top condition.
Use Predictive Maintenance Techniques: Leverage advanced technologies like vibration analysis, thermography, and oil analysis to monitor the condition of your motors. This data-driven approach enables you to predict and prevent failures.
Train Your Maintenance Team: Ensure your technicians are properly trained on the correct procedures for motor maintenance, troubleshooting, and repair. This will improve the quality and consistency of your preventive maintenance efforts.
Document and Analyze Performance Data: Meticulously record all maintenance activities, repairs, and performance data. Analyzing this information will help you identify trends, optimize your program, and make informed decisions about equipment replacement.
By implementing these proven strategies, you can develop a comprehensive preventive motor maintenance program that extends the lifespan of your equipment, reduces operating costs, and enhances the overall reliability of your facility.
The Financial and Operational Benefits of Proactive Motor Maintenance
Neglecting the maintenance of your motors can have serious financial and operational consequences for your business. Conversely, implementing a proactive motor maintenance program can yield significant benefits that extend far beyond just extending the lifespan of your equipment.
Reduced Downtime and Increased Productivity
Unplanned motor failures lead to unexpected downtime, which disrupts your operations and reduces productivity. Proactive maintenance helps you avoid these costly interruptions by identifying and addressing issues before they cause a breakdown. This keeps your motors running smoothly and your operations on track.
Lower Repair and Replacement Costs
Catching problems early through regular inspections and maintenance allows you to make minor adjustments or replace worn components before they cause catastrophic motor failure. This is far more cost-effective than waiting for a complete breakdown that requires a full motor replacement.
Improved Energy Efficiency
Well-maintained motors operate at peak efficiency, consuming less energy than motors that have fallen into disrepair. The energy savings from proactive maintenance can have a measurable impact on your utility bills over time.
Longer Motor Lifespan
By staying on top of maintenance, you can maximize the useful life of your motors, deferring the need for costly replacements. This preserves your capital equipment budget and gives you a better return on your initial motor investments.
Real-World Examples of Companies Transforming Their Motor Operations with Preventive Maintenance
Companies Transforming Motor Operations with Preventive Maintenance
Implementing a robust electric motor preventive maintenance strategy for your motor systems can yield significant operational and financial benefits. Consider these real-world examples of organizations that have reaped the rewards of proactive motor maintenance:
A large manufacturing facility reduced unplanned downtime by 35% after deploying predictive maintenance sensors on critical motors. By monitoring vibration, temperature, and other key parameters, they were able to identify issues early and schedule maintenance before failures occurred.
A municipal water treatment plant cut energy costs by 12% by optimizing motor efficiency through regular cleaning, lubrication, and alignment checks. This preventive approach extended the useful life of their motors and reduced the need for premature replacements.
In the mining industry, one company implemented a condition-based maintenance program that allowed them to extend the service life of their heavy-duty motors by an average of 30%. This translated to substantial savings in capital expenditures for new equipment.
The evidence is clear – companies across diverse sectors are transforming their motor operations and achieving meaningful results through the implementation of effective preventive maintenance practices. Investing in this proactive approach can deliver long-term dividends in the form of improved reliability, efficiency, and profitability.
Conclusion: Use Electric Motor Preventive Maintenance to Improve Operational Efficiencies
The evidence is clear – proactively managing your motor assets can unlock significant operational efficiencies and cost savings for your business. By implementing a comprehensive motor management program, you gain visibility and control over this critical equipment, allowing you to make data-driven decisions that optimize performance and minimize downtime.
Whether it’s leveraging predictive maintenance strategies, right-sizing your motor fleet, or tapping into energy-efficient technologies, the benefits compound quickly. Reduced energy bills, extended equipment lifespans, and streamlined maintenance workflows all contribute to a healthier bottom line.
The time to take action is now. Seize control of your motor assets and watch your organization soar to new heights of productivity and profitability. The path to optimized motor management is clear – all that’s left is for you to take the first step.